How to calibrate your turntable: Get the most from your vinyl with our step-by-step guide
A few simple steps is all that separates you from getting your turntable up to speed for optimal performance
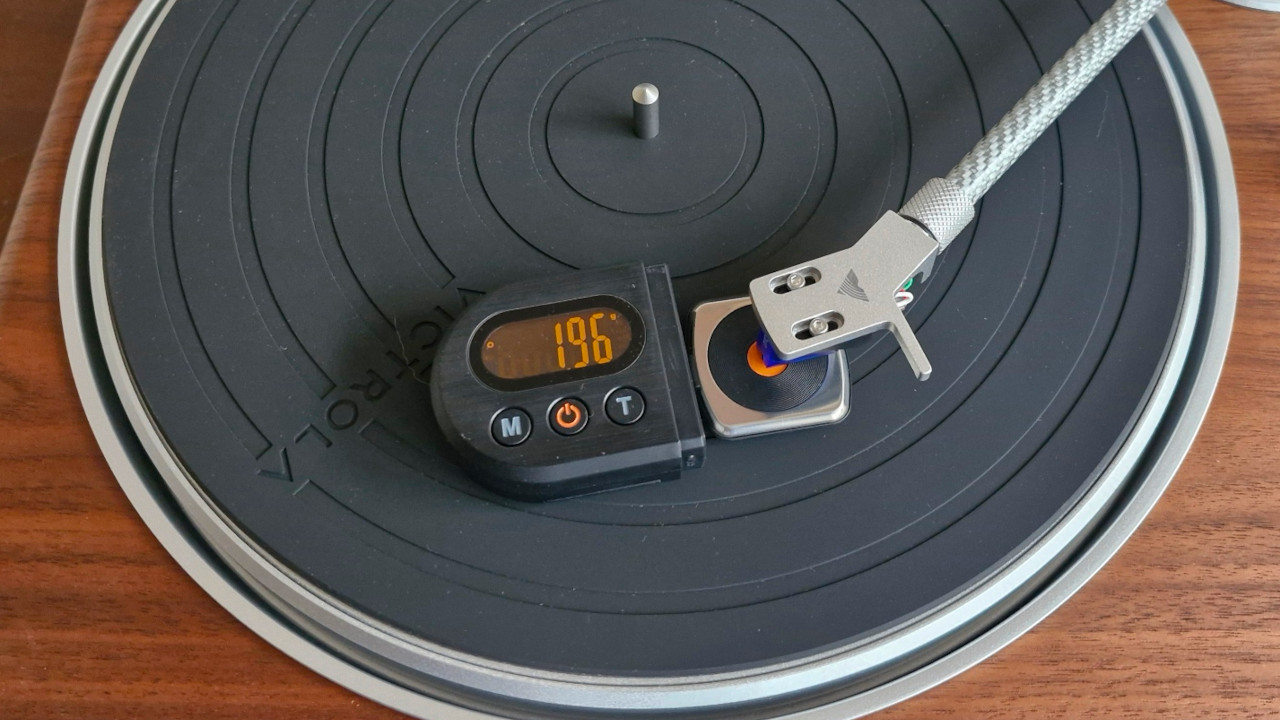
If you’re reading this, you’ve probably taken your second step into the world of turntable ownership recently. The first step is buying a record player, and the discovery of just how fun blasting records can be. The second is a slower, more furtive one, driven by the simple question: “Could my records sound better?”
There are many things that impact how good your vinyl sounds, and many will first look to the make-up of their hi-fi system for answers. But there’s an essential step you should be taking first to ensure your hi-fi and ears are receiving the audio they deserve.
Maybe you’ve bought a new turntable or invested in a vintage one. Maybe you’re installing a new cartridge on your existing turntable and need to set everything back up again. Whatever the reason – and even if there’s no reason – you should know how to calibrate your turntable. But why?
Why calibrate your turntable?
Turntables are not altogether complicated in design, construction or operation, but their performance is heavily impacted by a number of complicated-seeming variables. If your stylus isn’t where it should be, it could be wearing one side of your record groove out; if your tonearm’s weighing heavy on your record, you could be damaging both record and stylus.
Phasing, crosstalk, distortion, bounce-outs – these problems and more are all mitigated by calibrating your turntable, the results of which are like night and day.
What do you need?
First, you’ll need something called a tracking force gauge, for measuring the weight of your stylus as it applies to the records you play. Any digital scale with a precision of 0.01g will do here, but you can find quite a few cheap (and small) models online that are specifically designed for this task.
The next thing you’ll need is something called a cartridge alignment protractor. This is a measuring tool which sits on your turntable’s platter, anchored by the spindle, and which allows you to perform most of your cartridge alignment steps. There are a few different types you can get, and some you can print off yourself, which can use any of three different alignment standards - more on which later.
The latest news, features and interviews direct to your inbox, from the global home of alternative music.
Finally, you’ll need something called an azimuth ruler. This is typically a clear plastic or glass block which sits vertically on your platter, designed to butt up against the front of your cartridge and allow you to make tweaks to horizontality of your cartridge and tonearm.
Step 1
Set your tracking force
The tracking force is calibrated by adjusting the counterweight to the rear of your tonearm. Too light, and your stylus is more like to bounce out and skate around your record, risking damage. Too heavy, and your needle will actively abrade the interior surfaces of your groove, ruining your records and eventually ruining itself.
The ideal tracking force is defined by the cartridge you’re using. For instance, the ideal tracking force for an Audio-Technica VM-95E cart is between 1.8 and 2.2mm; as such, you’d be aiming for 2mm tracking force. Set your counterweight such that your tonearm is balancing on its pivot – and if it has a numbered indicator ring, set that to 0.
Now, place your tracking force gauge on the platter (ensuring its calibrated and properly zeroed), move your counterweight in a little, and set your stylus down on the gauge. Keep reseating the counterweight until you get the desired weight, and with that your tracking force will be set.
Step 2
Align your cartridge
To cut a long story short, your stylus’ relationship to the record groove changes as it sweeps into the centre. The more it changes, the more the sound of your records can be impacted, typically by distortion and harsh sibilance.
The ideal relationship between your stylus and groove is tangential – that is, that your stylus is neither digging inwards nor facing outwards. But with pivoting tonearms, this can only happen at two points on a given record. As such, you’re aligning your cartridge to get the best possible results, using these two ‘null points’ as a guide.
The position of these null points, and hence the sound of your record as a whole, is dependent on two things: stylus overhang, and alignment angle (or zenith angle). Your alignment protractor is your template for setting these, and will be itself calibrated to one of three standards: Baerwald, Stevenson and Lofgren B (though Technics turntables have their own calibration standard altogether). For most, the Baerwald standard is the happiest medium – and the standard used on most basic alignment protractors.
Place your protractor on the platter, loosen the screws holding your cartridge in place a little, and then pull your tonearm over to the first null point on the protractor. You want to line the stylus up with the dot at the centre, and then twist the cartridge so that the cantilever is parallel with the lines.
Lightly tighten it into place, then move the stylus over the second null point towards the centre – and repeat the same steps. Go back and forth until you’ve found a happy medium between the two, and bob’s your uncle!
Step 3
Set your cartridge azimuth
Your cartridge’s azimuth is how it sits horizontally when you face it end-on. Adjusting the azimuth fine-tunes how the stylus sits in the groove; you want the stylus to be vertical, and hence reading the left and right channels of encoded audio somewhat equally. If it isn’t vertical, you’ll get more crosstalk and a less focused stereo image in your speakers. For most systems, you won’t need to do much here, but for peace of mind, you can use an azimuth ruler to reference and adjust your cartridge against.
Butt your ruler up to the end of the cartridge and see if the cart lines up with the markings. If it doesn’t, shim one of the screws to tilt the cart. This isn’t the most accurate method, though, as most styli aren’t perfectly perpendicular to their respective cartridge body.
If you’re seriously serious about your hi-fi – or if you’ve invested in a high-quality line-contact stylus – you’ll want to measure the level of crosstalk in your turntable’s outputs with an oscilloscope or digital multimeter, and make more informed adjustments accordingly.
Step 4
Set your Vertical Tracking Angle (VTA)
The vertical tracking angle (VTA) is the angle made between your record and the cantilever that holds your stylus, adjusted by lifting or lowering the tonearm at its base. Some record-playing fossils would have you believe that setting it correctly is a matter of life and death. Luckily, it isn’t.
Each record has its own ‘ideal’ VTA relating to the way its master disc was cut – besides which, there are a great many variables, from the subtle warp of some records to the thickness of the vinyl itself. To maintain the ideal VTA, you’d be adjusting your tonearm height practically every time you changed the record – which some people do. Still, each to their own.
For most cases, you can safely set your tonearm to be pretty-much parallel with your record, in order to achieve an acceptable VTA; your azimuth ruler will also have long horizontal lines for checking VTA against, so use these to reference and set your tonearm angle.
I take a somewhat cavalier approach to VTA, as you may have surmised – but there are times it really does matter. Again, if you’ve invested in a line-contact stylus, you need to think a bit more carefully about VTA and its corresponding SRA (stylus rake angle), in order to ensure you’re getting the precision your stylus is capable of.
Step 5
Do it all again
Just kidding. Well, half-kidding. Every change you make will have knock-on impacts on other aspects of your calibration, most obviously with setting your stylus overhang and setting your tracking force. Thankfully, you won’t need to make any major moves – all you’re doing is making sure that everything’s still where you left it, and adjusting accordingly.
Step 6
Set your anti-skate
The final piece of the puzzle is your record player’s anti-skate – the outward-pushing mechanism that counters your tonearm’s desire to move itself towards the spindle during play. Most turntables have a dial for setting this, but some Pro-Ject turntables use a wire-suspended weight with a notched post for changing its leverage.
Many guides will tell you to set your anti-skate one-to-one with your cartridge’s recommended tracking force – and many seasoned audiophiles will tell you that 10% of your cartridge’s tracking force is closer to the money. The real answer is somewhere between these extremes, and a good rule of thumb would be: the costlier your cartridge, the less anti-skate you’re likely to need.
And that's it! It’s a bit of work getting a turntable fully calibrated, but that bit of effort is hugely worth it – whether improving the sound from your hi-fi, or simply protecting your records for the long-term. The next record you play will be reward enough for the sheer difference you’ll hear in your system.
Related content
- How to can safely install or replace a turntable cartridge
- Does vinyl really sound better than other formats?
- CD vs vinyl: Which sounds better and why it matters
- Cool vinyl record storage ideas
- How to store vinyl: Tips on keeping your collection in great condition
- Direct-drive vs belt-drive turntables: What's the difference?
- Best vinyl record cleaners: Keep your vinyl collection in prime condition
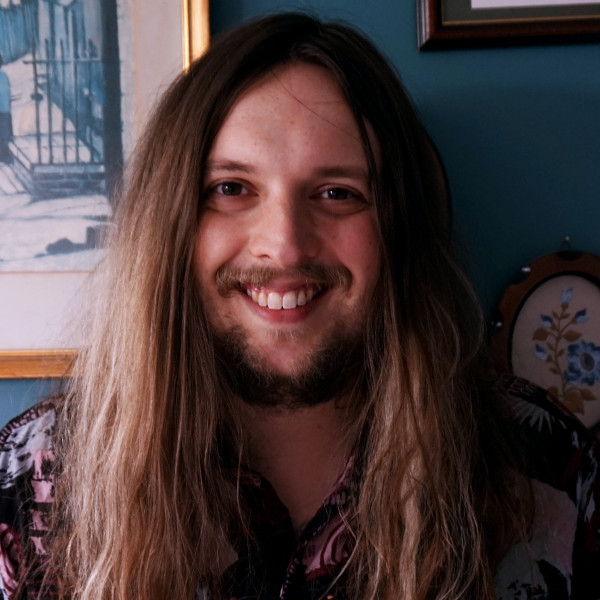
James Grimshaw is a freelance writer and music obsessive with over a decade in music and audio writing. They’ve lent their audio-tech opinions (amongst others) to the likes of Guitar World, MusicRadar and the London Evening Standard – before which, they covered everything music and Leeds through their section-editorship of national e-magazine The State Of The Arts. When they aren’t blasting esoteric noise-rock around the house, they’re playing out with esoteric noise-rock bands in DIY venues across the country; James will evangelise to you about Tera Melos until the sun comes up.